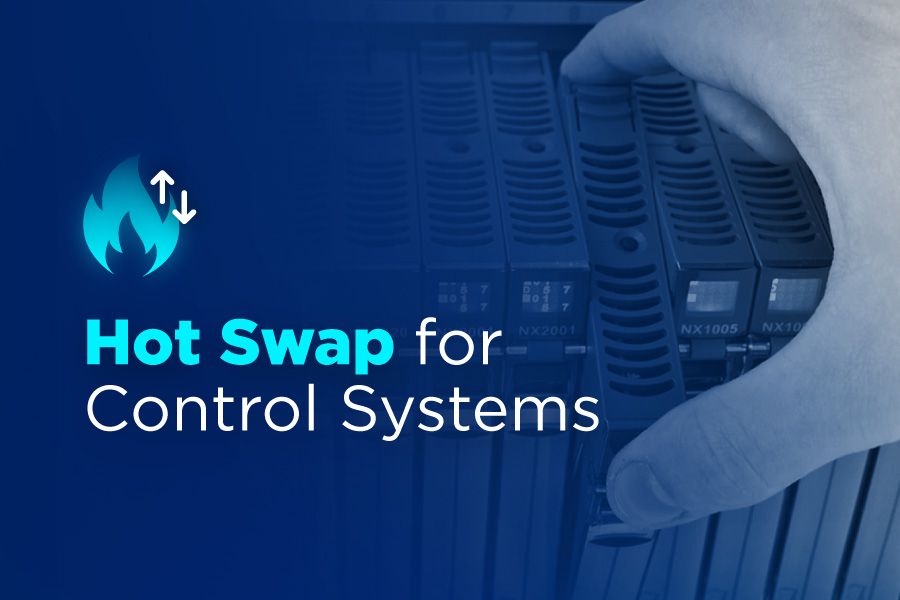
The Impact of Hot-Swap Technology on Control Systems
Ensuring the continuity of the production process has become essential for maintaining industry competitiveness in today`s highly competitive market. In this context, hot swap technology acts as a differentiating factor, reducing process downtime and ensuring business productivity and efficiency.
In this article, we will explore the concept of hot-swapping, its impact on industrial productivity, and its importance in increasing the availability of control and supervision systems in production units.
What is Hot-Swapping?
An essential feature in industrial control and supervision systems, hot-swapping is a functionality that allows the replacement or addition of components in electronic systems without the need to shut down the equipment. This capability is particularly useful for machines and processes in large production units, where any downtime can result in high costs and loss of productivity. Hot swapping allows smooth transitioning without operational interruptions. This capability distinguishes it from the traditional "cold swapping" approach, which requires the system to be shut down to make hardware changes.
In practice, hot-swapping is enabled through an integrative design that includes special circuits and control software. These systems are designed to detect the connection or disconnection of components automatically, configuring them in real-time. This architecture eliminates the risk of damage to electronic components or system failures due to power interruptions. Moreover, the hot-swap feature allows regular maintenance and upgrades, which are crucial for maintaining operational efficiency and extending the equipment`s lifespan.
This concept of high availability, a critical factor in industrial automation, ensures that machines and systems remain operational for as long as possible. The adoption of hot swap technologies in control and supervision systems significantly increases system availability by allowing maintenance and expansion of operations with no stops. This feature prevents financial losses and increases the operator’s confidence in the safe and continuous performance of machines and processes.
What is Availability in Industrial Automation?
In the context of industrial automation, availability refers to a system`s ability to operate without major interruptions. This concept is directly related to the reliability and performance of the equipment. To maximize this availability, technologies such as hot-swapping are essential, as they allow maintenance and upgrades without shutting down the system.
Availability is often confused with fault tolerance, but these are completely different concepts. While availability refers to reducing and managing downtime for maintenance or problem correction, fault tolerance concerns a system`s ability to continue operating even when a component fails. Hot-swapping works with both concepts, reducing application downtime and allowing quick hardware replacements in case of failure, ensuring the system to returns to normal operations as quickly as possible.
In this way, hot swapping not only increases the availability of automation systems but also contributes to their high reliability and ruggedness , making industrial operations more efficient and less susceptible to interruptions.
See also: The importance of Conformal Coating in industrial electronic products
The Importance of Hot-Swapping in Industry
As explained in the previous paragraphs, hot swapping is an essential feature in modern industrial facilities, as it plays an important role in process optimization and cost reduction. To help better illustrate the relevance of the feature, we have selected five points that highlight its importance for the industry:
Minimizing Downtime: Replacing defective components or implementing improvements without shutting down the system avoids production interruptions. This allows operations to continue without stops, increasing production and avoiding financial losses.
Increased operational efficiency: Hot swapping makes maintenance interventions faster and less invasive. This allows technicians to repair or upgrade more frequently, ensuring that systems operate at full capacity.
Reduced maintenance costs: The functionality allows components to be replaced without the need to interrupt machine operation, saving time and labor.
Flexibility and Scalability: Hot-swapping enables new features or functionalities to be added to the existing system without making major infrastructure changes. This allows companies to quickly adapt to production demands or new technologies.
Improving Safety and Reliability: Implementing hot-swapping reduces the likelihood of startup errors and failures related to frequent restarts, as it decreases the number of times systems need to be shut down and restarted for maintenance.
Industrial Sectors Where Hot-Swapping is Essential
Hot-swapping is a vital technology in various industrial sectors where operational continuity and efficiency are paramount. Below, we list five segments where this functionality is particularly crucial.
Petrochemical: In petrochemical plants, where process continuity is essential, hot-swapping allows the maintenance of control systems without interrupting production, mitigating the risk of costly downtime and increasing operational safety.
Power: In the power sector, especially in power plants and substations, the ability to perform maintenance or replacements without turning off equipment is essential to ensure continuous power delivery and prevent supply failures.
Water & Wastewater: In the water and wastewater segment, hot swapping is essential to ensure continuous water treatment and distribution operations, allowing maintenance on control systems without interrupting services.
Transportation: In traffic control systems or railway operations, hot swapping ensures that updates and maintenance do not disrupt transportation services, which is critical for safety and logistics.
Healthcare: Medical equipment and monitoring systems in hospitals benefit from hot swapping to ensure that patient care is not compromised during critical maintenance or system updates.
The Advantage of Using a Hot-Swap Enabled PLC
Responsible for actuation devices, monitoring variables, collecting data, communicating with supervisory systems, and many other processes in a control architecture, programmable controllers are crucial for the stability of an industry`s operation. By using PLCs with support for hot swap technology, you add even more availability to the system, protecting your operation against unexpected downtime and accelerating maintenance routines.
In systems equipped with hot-swap technology, controllers can automatically recognize and configure new modules or components as soon as they are connected, without the need for interruptions. This not only minimizes downtime but also ensures that changes are implemented quickly and safely.
In addition, many modern PLCs, such as the Nexto Series programmable controllers, offer embedded diagnostic and monitoring functionalities. These features make the detection of faults much easier with replacement of modules in real time, strengthening the system`s ability to maintain continuous and efficient operations.
In the event of a faulty I/O module detection, the use of Altus equipment with hot-swap support, allows the user to remove the defective module and replace it with a new one while the system remains operational. In this case, the PLC automatically detects the new module, recalibrates the necessary settings, and continues to execute the program without errors or delays.
However, it is not just during failure moments that the hot-swap feature is essential for an industrial application. When there is a need to add advanced control modules to optimize energy efficiency or process accuracy, this insertion can be done without interrupting the machine’s operation.
Ensure Your Operation`s Availability with the Nexto PLC
Developed to meet the diverse demands of the industry, the programmable controllers from the Nexto Series support hot-swapping in their main I/O modules. Rugged and with a wide variety of options, the Nexto Series input and output modules can be replaced without the need to de-energize the system. This feature allows the CPU to maintain control of the entire process, and the Nexto modules can be replaced while the plant is still operating.
Discover Nexto technology and find out how our PLCs can ensure high productivity and total availability for your production system.