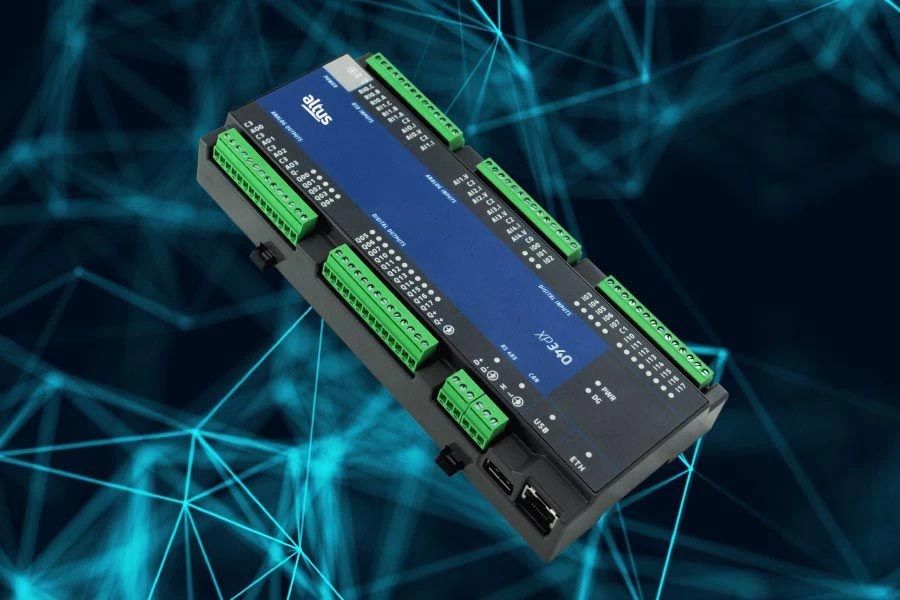
Xpress PLC gets new features for CAN interface
The release of XP340, PLC with WebServer support, isn’t the only new feature of the Nexto Xpress line for this holiday season. In addition to the new member, Altus` compact programmable controllers family has also gained two features that can further extend its range. Now, Xpress devices have the capacity to develop low level protocols and expand its inputs and outputs via CAN interface.
The controllers in the Xpress solution count on a CAN 2.0A and CAN 2.0B compliant CAN bus interface (11 and 29-bit identifiers). There are two traditional use cases for this interface: with the CANopen Manager protocol, which allows the PLC to communicate with CANopen slave I/O devices, and with the CANopen Slave operating mode, used in applications where the PLC acts as a secondary I/O device. In addition to these two cases, we can also use the interface for low level CAN communication.
Low level protocols development
To allow the information exchange between the components of a network to occur in an orderly manner, a number of protocols are stablished to define the rules to be used when communicating between the components. There, each subnet interface is responsible for implementing the medium access protocol that controls its transmissions, the link protocol that regulates communication between interfaces and the network access protocol that specifies and polices interactions between the interface and your username. These protocols within the communication subnet scope are called low-level protocols.
Low-level CAN communication allows the PLC to transmit and receive raw CAN messages without using upper layer protocols such as CANopen, which can be useful for communicating with devices using custom protocols. These features are available on all models of the Nexto Xpress line from firmware version 1.8.5.0 and MasterTool IEC XE 3.19.
The CANOpen Protocol
Created in 1994 by a group of companies, CANOpen is one of the most complete and diverse Industrial Networks in the market today. By operating in a multi-master communication standard, the network meets markets with the highest data complexity and security requirements, such as medical, rail and naval navigation. Based on CAN Network Technology - created in the 1980s for use in truck, bus and car embedded systems - the standard presents itself as a low cost open industrial network for complex applications.
The multi-master model used by the standard makes communication between application devices faster and simplifies network flow. The modularization of the network also brings benefits in the installation, refurbishment and implementation of equipment and new field components up to the limit number of ASi Network slaves (31 slaves). In addition, the protocol is standardized according to IEC, ISO and ITU criteria, with its application layer being defined in EN 50325-4.